Manufacturing for New Era
Embracing Technology for Smarter Factories
Posted On
24-12-12 下午12:30
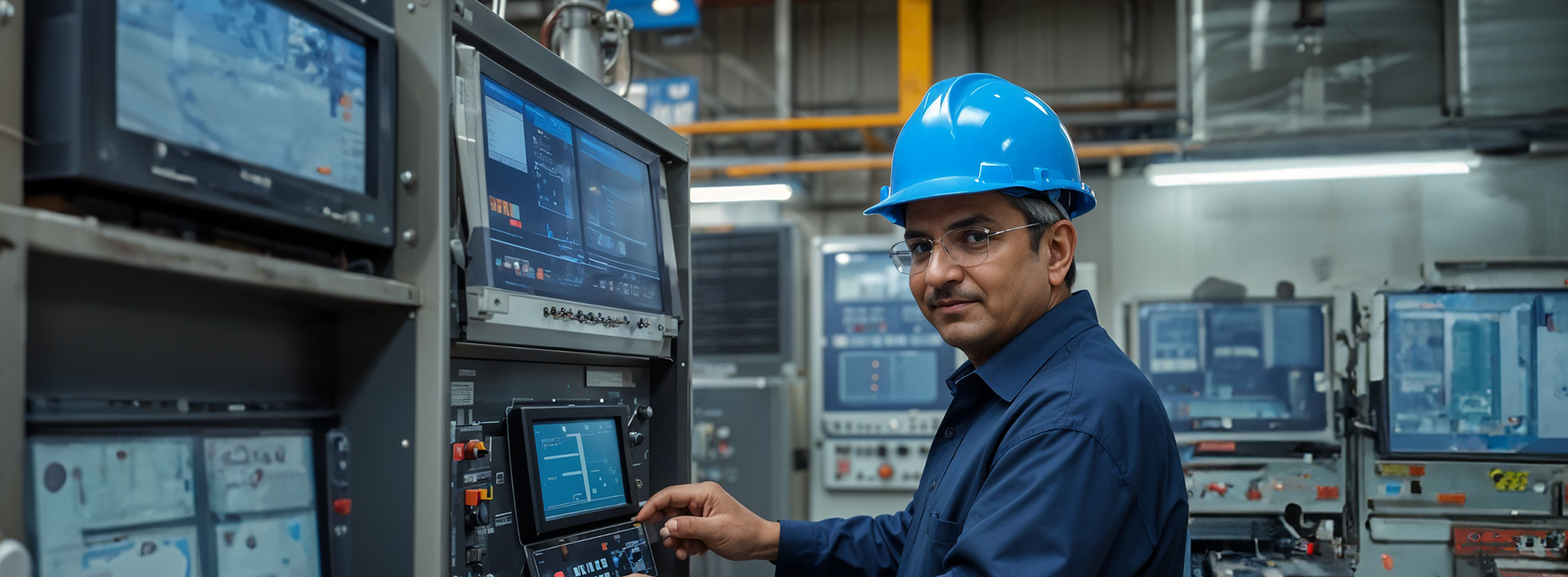
In today’s fast-evolving industrial landscape, traditional manufacturing methods are increasingly inadequate to meet the demands of efficiency, precision, and scalability. The new era of manufacturing demands a tech-oriented approach—a rethinking of the shop floor, weighbridge operations, workforce surveillance, and material management. Enter the concept of the Smart Factory: an environment where digital technology optimizes operations and decision-making.
What Makes a Factory Smart?
A Smart Factory isn’t just about automation; it’s a holistic integration of technology, data, and people. Below are the pillars that define a Smart Factory
1. Connectivity: The IoT Backbone
Smart Factories thrive on connectivity. Machines, devices, and systems are interconnected through the Internet of Things (IoT), enabling real-time data sharing. Sensors on equipment collect and transmit data, providing insights into performance, maintenance needs, and productivity. In Bosch’s Automotive Electronics Plant, IoT-enabled sensors provide real-time updates on machine performance, reducing downtime by 20% (Source: Bosch).
2. Data-Driven Decision-Making
Coca-Cola used AI-powered data analytics in their bottling plants to optimize water usage, achieving a 35% reduction in waste (Source: Coca-Cola Sustainability Report). A Smart Factory leverages data analytics to make informed decisions. Advanced analytics and AI process massive volumes of data to identify trends, predict failures, and optimize operations. This eliminates guesswork and ensures precision.
3. Automation and Robotics
Automation goes beyond replacing manual labor; it enhances consistency and efficiency. Robots and autonomous systems manage repetitive tasks, reducing human error and boosting output quality. Amazon’s fulfillment centers use robots to handle inventory storage and retrieval, cutting operational time by 40% (Source: Amazon Robotics).
4. Predictive Maintenance
Traditional factories rely on reactive maintenance, where repairs occur after a failure. Smart Factories, however, use predictive maintenance powered by AI and machine learning. This approach identifies potential issues before they escalate, reducing downtime and saving costs. Predictive maintenance can reduce unplanned downtime by up to 50% and maintenance costs by 30% (Source: Deloitte).
5. Workforce Augmentation with Technology
In a Smart Factory, technology supports—not replaces—the workforce. Augmented reality (AR) and virtual reality (VR) tools assist employees in complex tasks, training, and troubleshooting. Boeing uses AR glasses for assembly processes, reducing errors and improving efficiency by 25% (Source: Boeing AR Innovations).
6. Sustainability and Energy Efficiency
According to the World Economic Forum, Smart Factories can reduce carbon emissions by up to 37% compared to traditional setups (Source: WEF). Smart Factories prioritize sustainability by optimizing energy consumption and reducing waste. Energy-efficient systems and renewable energy integration make operations environmentally friendly.
But how does one transition from conventional processes to a Smart Factory? Here’s a roadmap for organizations ready to take the leap.
Steps to Embark on a Smart Factory Journey
1. Identify Requirements and Involve Stakeholders
No two factories are alike. Begin by identifying what makes a factory smart for your specific unit. Engage key stakeholders, from shop floor operators to IT experts, to understand challenges and expectations.
For example, you are a global food manufacturer that sought to digitize its weighing processes. By involving weighbridge operators early on, you identify inefficiencies in manual data entry, leading to a tailored digital weighing solution.
2. Conduct Root Cause Analysis (RCA)
Identify bottlenecks—both existing and potential. Bottlenecks may include delayed workflows, equipment downtimes, or workforce inefficiencies. Conducting an RCA ensures you tackle pain points directly. According to McKinsey, bottleneck resolution in manufacturing can increase throughput by up to 30% without additional capital investment (Source: McKinsey & Company).
3. Digitize Processes with High ROI Potential
Prioritize processes that will yield the highest returns when digitized. These could include real-time production monitoring, predictive maintenance, or automated inventory tracking.
4. Start Small and Scale Gradually
Implementing Smart Factory technologies doesn’t have to be overwhelming. Begin with a pilot project—often called a Minimum Viable Product (MVP)—in controlled conditions.
Tip: Choose a process where the impact of improvement is measurable and scalable.
GE Aviation implemented predictive maintenance on a single line of jet engine parts. After validating the results, they scaled the technology across global operations, saving millions in unplanned downtime (Source: General Electric Reports).
5. Validate and Assess the Results
Analyze the performance of the MVP. Evaluate its impact on cost, productivity, and employee satisfaction. Use these insights to fine-tune the approach before scaling.
How Appvista Can Help
As an industry leader in technology-driven transformation, Appvista specializes in equipping businesses with the tools they need to transition to Smart Factories. Here’s how we can assist:
- Tailored Digital Solutions
We design and implement customized IoT, AI, and data analytics systems for shop floors, weighbridge operations, and workforce management, ensuring seamless integration with your existing processes.
- Risk Assessment and RCA
Our experts conduct thorough root cause analyses to identify bottlenecks and provide actionable recommendations, minimizing operational disruptions.
- Digitized Process Implementation
From predictive maintenance to real-time production monitoring, we help digitize processes with high ROI potential, improving operational efficiency.
- MVP Development and Scaling
Appvista guides businesses through pilot projects, helping evaluate results before scaling solutions company-wide.
- End-to-End Support
With our holistic approach, we provide ongoing technical support, training, and process optimization, ensuring long-term success.
The Future of Manufacturing is Here
The shift to Smart Factories isn’t just about keeping up with the times—it’s about future-proofing your business. By leveraging advanced technologies, manufacturers can:
Enhance productivity
Reduce operational costs
Improve safety and compliance
Boost employee morale through better tools
According to PwC, manufacturers who adopt smart technologies see an average productivity improvement of 30% and a cost reduction of 20% within the first two years (Source: PwC Smart Manufacturing Report).
Conclusion
The journey to a Smart Factory begins with a clear strategy: identify needs, involve stakeholders, analyze bottlenecks, and implement technology with precision. The path may seem complex, but the rewards—efficiency, agility, and profitability—are well worth it.
Start small, stay agile, and watch as your factory transforms into a hub of innovation.
For an optimal experience, please
rotate your device to portrait mode.